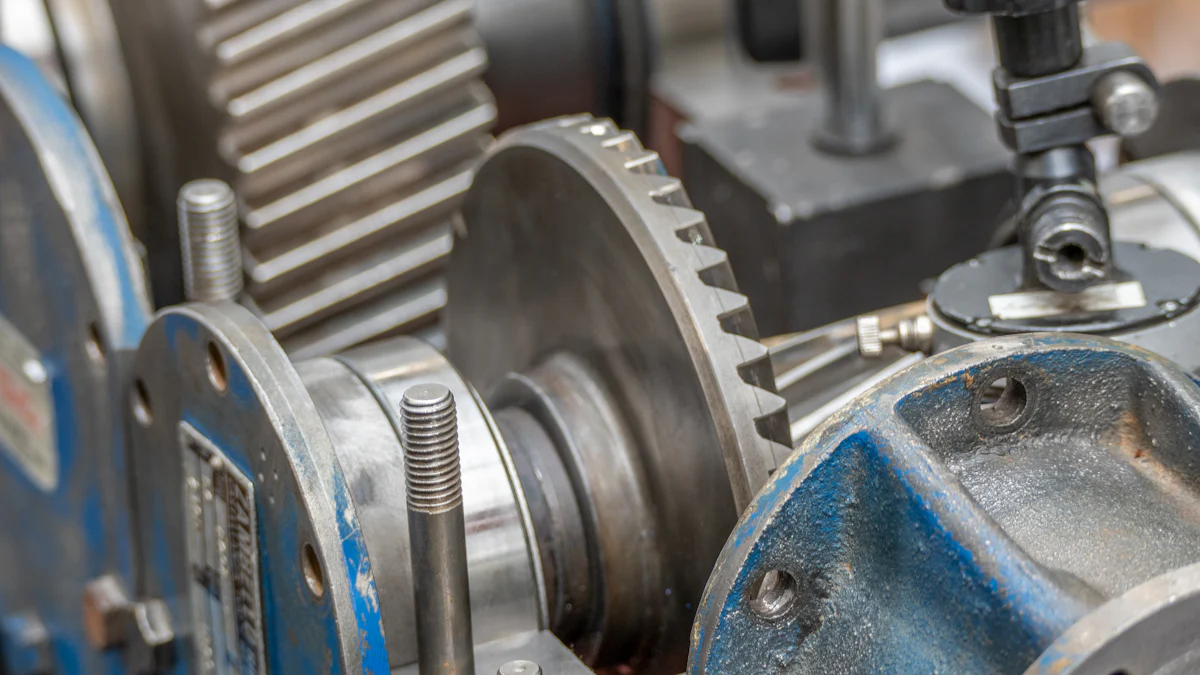
Staying updated with the latest trends in injection molding technology is crucial for anyone involved in the industry, including plastic injection molding machine manufacturers. These advancements not only enhance productivity but also shape the future of manufacturing. For instance, automation and robotics can boost productivity by about 15%. The sector is expected to grow annually by 4-5% from 2023 to 2028, driven by industries like automotive and packaging. So, what are the latest innovative trends in plastic injection molding machine technology? Let’s dive in and explore how these changes are revolutionizing the field.
Technological Innovations in Plastic Injection Molding Machine Manufacturers
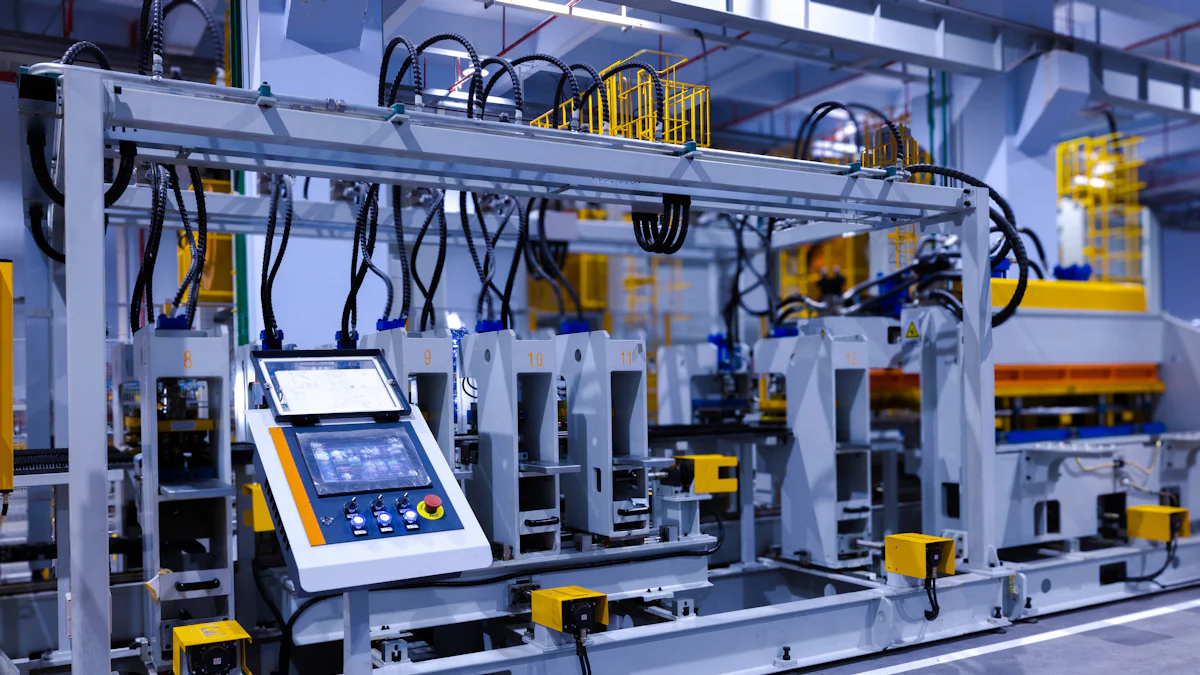
In the ever-evolving world of manufacturing, Plastic Injection Molding Machine Manufacturers are at the forefront of technological innovation. They are constantly integrating cutting-edge technologies to enhance efficiency and precision. Let’s explore some of these groundbreaking advancements.
AI Integration
Artificial Intelligence (AI) is transforming the landscape of plastic injection molding. By incorporating AI, manufacturers can achieve unprecedented levels of efficiency and accuracy.
Predictive Maintenance
AI-driven predictive maintenance is a game-changer for Plastic Injection Molding Machine Manufacturers. By analyzing data from sensors and machine components, AI can predict when a machine might fail. This proactive approach minimizes downtime and reduces maintenance costs. Manufacturers can schedule maintenance activities at optimal times, ensuring machines run smoothly without unexpected interruptions.
Process Optimization
AI also plays a crucial role in process optimization. It analyzes vast amounts of data to identify patterns and suggest improvements. This leads to more efficient production cycles and higher-quality products. Plastic Injection Molding Machine Manufacturers can fine-tune their processes, reducing waste and enhancing overall productivity. The integration of AI ensures that every aspect of the molding process is optimized for maximum efficiency.
Automation and Robotics
Automation and robotics are revolutionizing the injection molding industry. They bring precision and speed to the manufacturing process, allowing manufacturers to meet the demands of modern markets.
Enhanced Precision
Robots equipped with advanced vision systems handle parts with incredible precision. This reduces error rates and ensures consistent product quality. Plastic Injection Molding Machine Manufacturers benefit from robots that can perform tasks with a level of accuracy that surpasses human capabilities. This precision is vital in industries where even the smallest deviation can lead to product failure.
Increased Production Speed
Automation significantly boosts production speed. Robots can work tirelessly, performing repetitive tasks without fatigue. This leads to faster production cycles and increased output. Plastic Injection Molding Machine Manufacturers can respond quickly to market demands, producing large quantities of products in a short time. The ability to switch between molds quickly further enhances production flexibility, allowing manufacturers to adapt to changing consumer needs.
Sustainability in Injection Molding
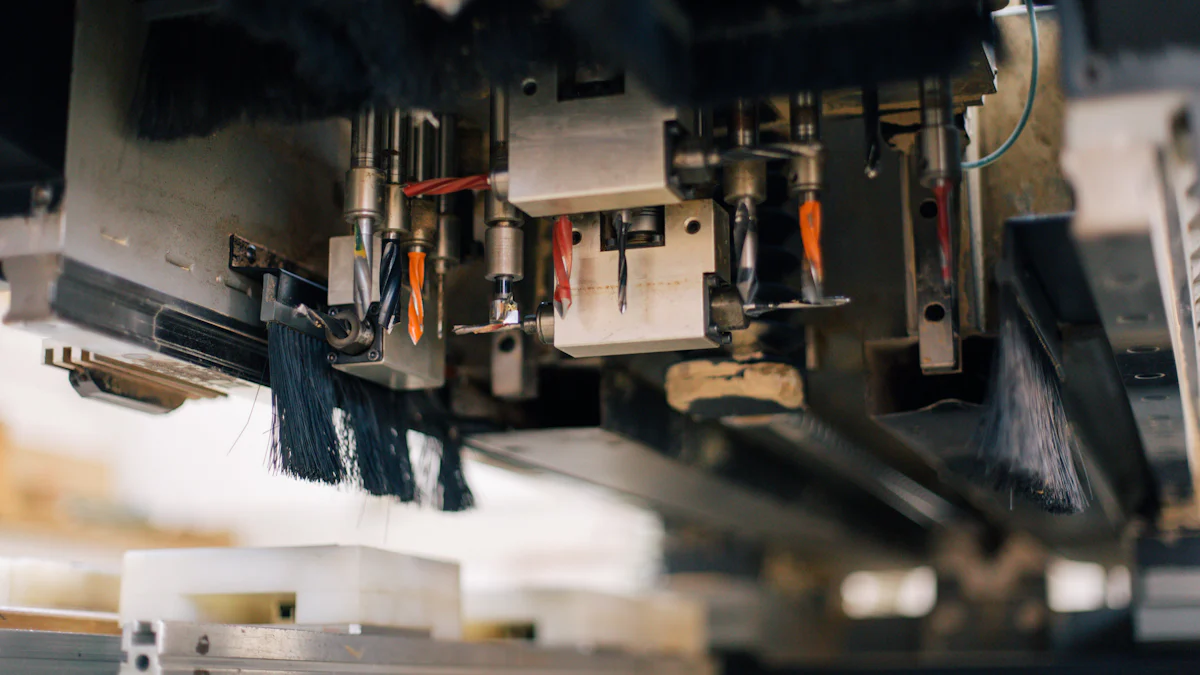
Sustainability has become a buzzword in the injection molding industry. Manufacturers are increasingly focusing on eco-friendly practices to meet regulatory requirements and consumer expectations. Let’s explore how energy efficiency and eco-friendly materials are driving this shift.
Energy Efficiency
Energy efficiency is a top priority for manufacturers aiming to reduce operational costs and environmental impact. By adopting energy-efficient technologies, they can achieve significant savings and enhance competitiveness.
Use of Electric Machines
Electric machines are revolutionizing the injection molding process. Unlike traditional hydraulic machines, electric machines consume less energy and offer greater precision. They operate with high efficiency, reducing energy consumption by up to 50%. This not only lowers electricity bills but also minimizes the carbon footprint. Manufacturers benefit from faster cycle times and improved product quality, making electric machines a smart investment for sustainable production.
Energy Recovery Systems
Energy recovery systems are another innovative approach to enhancing energy efficiency. These systems capture and reuse energy generated during the molding process. By converting excess heat into usable energy, manufacturers can further reduce energy consumption. This leads to cost savings and supports sustainability goals. Energy recovery systems exemplify how technology can transform waste into valuable resources, promoting a circular economy in the injection molding industry.
Eco-friendly Materials
The use of eco-friendly materials is gaining momentum as manufacturers strive to minimize environmental impact. By incorporating biodegradable and recycled materials, they can produce sustainable products that align with consumer preferences.
Biodegradable Plastics
Biodegradable plastics are a game-changer in the quest for sustainability. These materials break down naturally over time, reducing plastic waste in landfills. Manufacturers are developing biodegradable polymers that maintain the performance characteristics of traditional plastics. This innovation allows for the creation of products that are both functional and environmentally friendly. As demand for sustainable products grows, biodegradable plastics offer a viable solution for reducing plastic pollution.
Recycled Materials
Recycled materials play a crucial role in sustainable injection molding. By using recycled plastics, manufacturers can reduce the need for virgin materials and decrease environmental impact. This approach supports the circular economy by giving new life to discarded plastics. Recycled materials are increasingly being used in various applications, from packaging to automotive parts. By embracing recycled materials, manufacturers can meet sustainability targets while delivering high-quality products.
Material Advancements
The world of plastic injection molding is buzzing with exciting developments in material science. Engineers and material scientists are pushing the boundaries, creating materials that are not only more efficient but also environmentally friendly. Let’s explore some of these advancements.
High-performance Polymers
High-performance polymers are making waves in the industry. These materials offer enhanced properties that cater to a wide range of applications.
Heat-resistant Materials
Heat-resistant materials are crucial for industries that require durability under extreme conditions. Traditional plastics often fall short when exposed to high temperatures. However, high-performance polymers withstand heat, maintaining their integrity and performance. This makes them ideal for automotive and aerospace applications, where heat resistance is paramount. By using these advanced materials, manufacturers can produce components that last longer and perform better.
Lightweight Composites
Lightweight composites are another game-changer. They combine strength with reduced weight, offering significant advantages over traditional materials. In sectors like automotive and aerospace, reducing weight translates to improved fuel efficiency and performance. These composites maintain the necessary strength while cutting down on bulk. Manufacturers benefit from materials that enhance product performance without compromising on quality.
Smart Materials
Smart materials are revolutionizing the way products are designed and manufactured. These materials respond to environmental changes, offering unique benefits.
Self-healing Polymers
Imagine a material that can repair itself after damage. Self-healing polymers do just that. They have the ability to mend cracks and breaks, extending the lifespan of products. This innovation reduces the need for replacements and repairs, saving both time and resources. Industries like electronics and automotive are exploring these polymers to enhance product durability and reliability.
Conductive Plastics
Conductive plastics are opening new doors in the world of electronics. These materials conduct electricity, allowing for innovative applications in electronic devices. They offer flexibility and lightweight properties, making them ideal for wearable technology and flexible circuits. By incorporating conductive plastics, manufacturers can create products that are both functional and versatile.
Market Dynamics in Plastic Injection Molding Machine Manufacturers
The landscape of plastic injection molding is constantly evolving, influenced by global market trends and technological advancements. Understanding these dynamics is crucial for manufacturers aiming to stay competitive and innovative.
Global Market Trends
The global market for plastic injection molding machines is experiencing significant shifts. Emerging markets are at the forefront of this growth, driven by increasing industrialization and demand for consumer goods.
Growth in Emerging Markets
Emerging markets, particularly in Asia and Latin America, are witnessing rapid expansion. These regions offer vast opportunities for Plastic Injection Molding Machine Manufacturers due to their growing economies and rising consumer demand. As industries like automotive and electronics expand, the need for efficient and cost-effective manufacturing solutions increases. Manufacturers are capitalizing on these opportunities by establishing production facilities and forming strategic partnerships in these regions.
Impact of Trade Policies
Trade policies play a pivotal role in shaping the global market dynamics. Changes in tariffs and trade agreements can significantly impact the cost and availability of raw materials and finished products. Plastic Injection Molding Machine Manufacturers must navigate these complexities to maintain competitiveness. By staying informed about policy changes and adapting their strategies accordingly, manufacturers can mitigate risks and seize new opportunities in the global market.
Industry 4.0
Industry 4.0 is revolutionizing the manufacturing sector, and plastic injection molding is no exception. This new era of smart manufacturing leverages advanced technologies to enhance efficiency and precision.
Digitalization of Manufacturing
Digitalization is transforming how manufacturers operate. By integrating digital technologies, Plastic Injection Molding Machine Manufacturers can streamline their processes and improve product quality. Digital twins, IoT devices, and cloud computing enable real-time monitoring and control of production lines. This connectivity allows manufacturers to optimize operations, reduce downtime, and respond swiftly to market demands.
Real-time Data Analytics
Real-time data analytics is a game-changer for the industry. By analyzing data from sensors and machines, manufacturers gain valuable insights into their operations. This data-driven approach enables predictive maintenance, reducing unexpected breakdowns and extending machine lifespan. Plastic Injection Molding Machine Manufacturers can make informed decisions, enhance process efficiency, and deliver high-quality products consistently. The integration of real-time analytics ensures that manufacturers remain agile and responsive in a rapidly changing market.
The plastic injection molding industry is undergoing a significant transformation. Key trends like AI integration, automation, and sustainability are reshaping the landscape. These advancements highlight the industry’s continuous evolution. As technology progresses, manufacturers must stay informed to remain competitive. The future looks promising, with smart manufacturing solutions and eco-friendly practices taking center stage. Businesses that adapt to these changes will thrive in this dynamic environment. Staying updated with these trends is not just beneficial—it’s essential for success in the ever-evolving world of injection molding.
Post time: Nov-22-2024