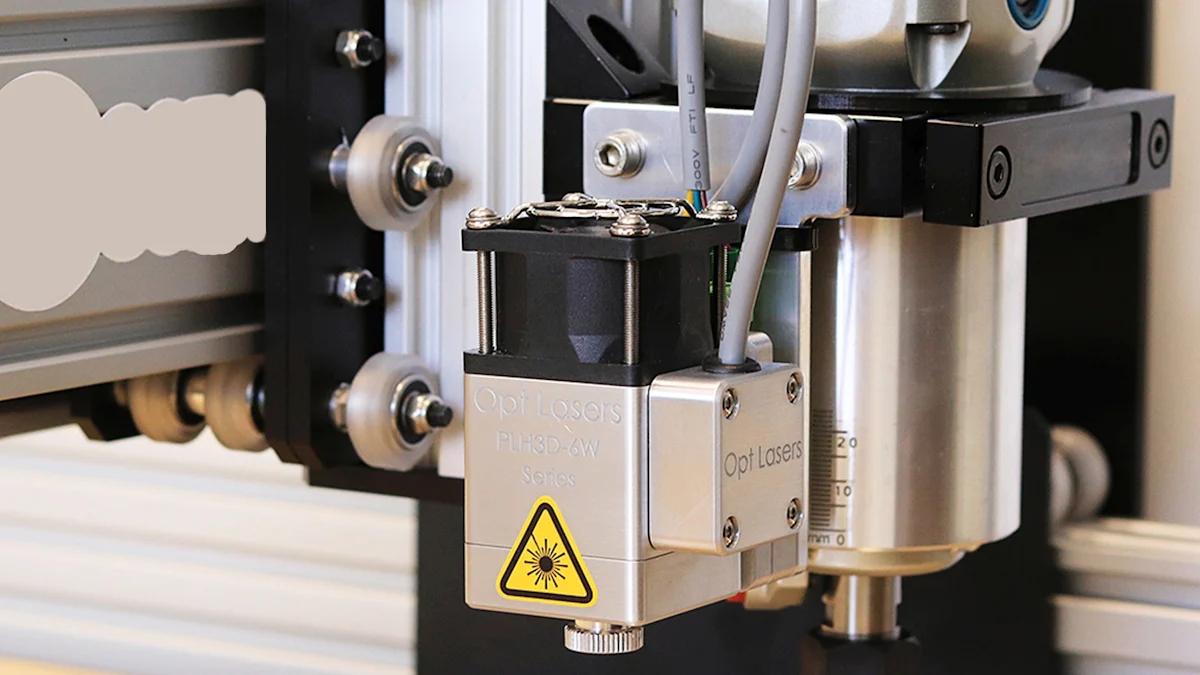
When you explore the world of plastic injection molding machine manufacturers in China, you’ll notice distinct differences compared to global counterparts. Chinese manufacturers often offer competitive pricing due to their extensive production capabilities. They excel in providing cost-effective solutions, making them appealing for businesses seeking affordability. However, global manufacturers, especially from Europe and Japan, lead in high-end technology and quality. These differences significantly impact your decision-making in the manufacturing sector. Understanding these variations helps you choose the right partner for your specific needs, balancing cost, quality, and technological advancement.
Overview of Injection Molding Machines
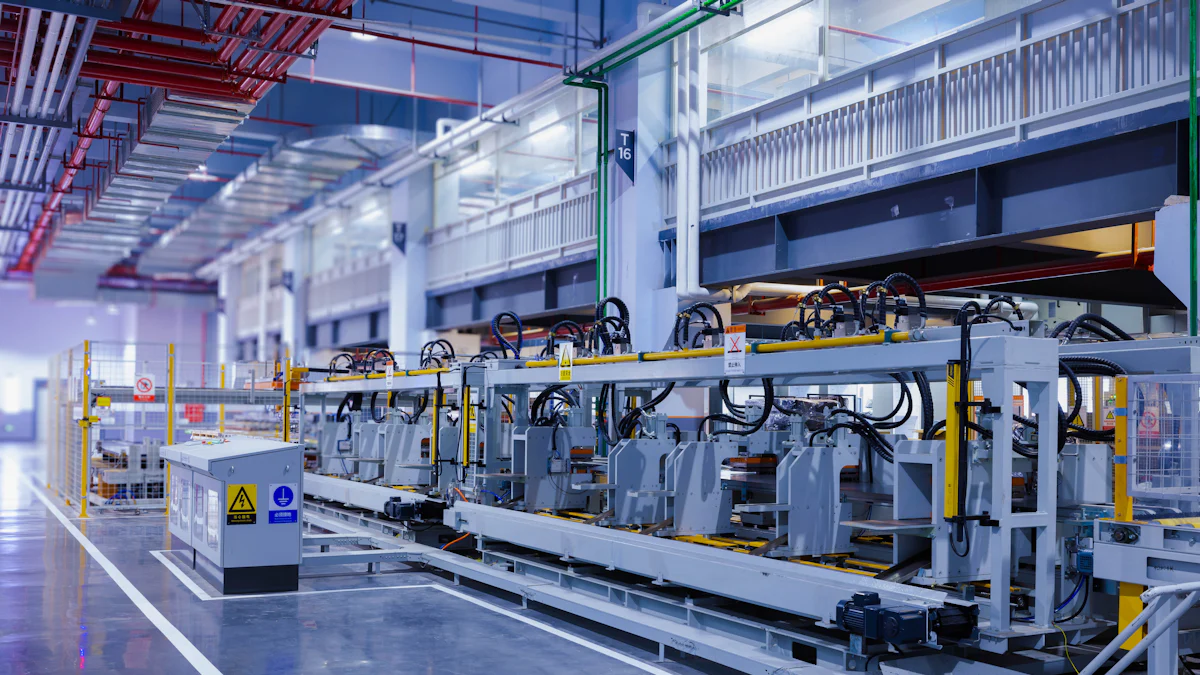
Definition and Function
Injection molding machines play a crucial role in manufacturing. They create plastic parts by injecting molten material into a mold. You can think of them as the backbone of plastic production. These machines ensure precision and efficiency, making them indispensable in various industries. By understanding their function, you gain insight into how everyday items are made.
Types and Applications
Injection molding machines come in different types, each serving specific purposes. Here are the main types you should know:
-
Hydraulic Injection Molding Machines: These machines use hydraulic power to operate. They are versatile and handle a wide range of materials. You often find them in industries requiring high-pressure molding.
-
Electric Injection Molding Machines: These machines rely on electric motors. They offer precision and energy efficiency. If you prioritize speed and accuracy, electric machines are ideal.
-
Hybrid Injection Molding Machines: Combining hydraulic and electric features, hybrid machines provide the best of both worlds. They offer flexibility and efficiency, making them suitable for diverse applications.
Applications of injection molding machines span various sectors:
-
Automotive Industry: You see these machines producing car parts like dashboards and bumpers.
-
Consumer Goods: Items like toys, containers, and household products often come from injection molding.
-
Medical Devices: Precision is key in medical equipment, and injection molding ensures high-quality production.
Understanding these types and applications helps you appreciate the versatility and importance of injection molding machines in modern manufacturing.
Plastic Injection Molding Machine Manufacturers in China
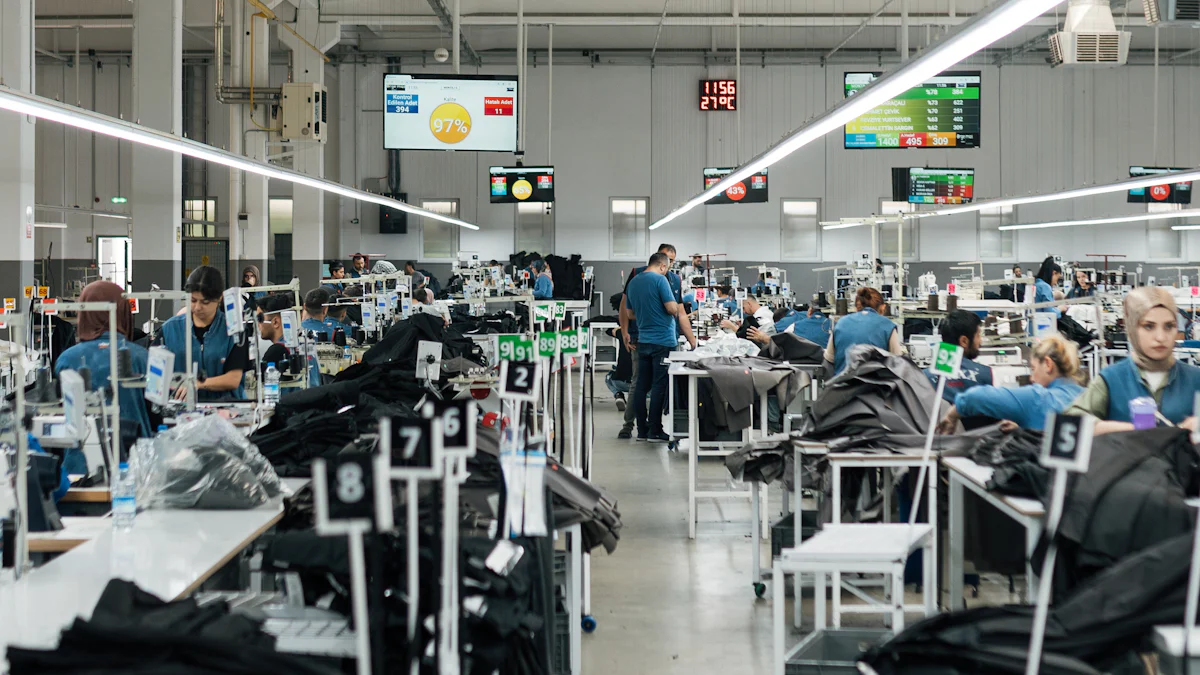
Strengths
When you consider plastic injection molding machine manufacturers in China, several strengths stand out. First, these manufacturers offer competitive pricing. Their extensive production capabilities allow them to produce machines at lower costs. This affordability makes them an attractive option for businesses looking to reduce expenses.
Second, Chinese manufacturers excel in scalability. They can handle large orders efficiently, which is crucial for companies with high production demands. You benefit from their ability to meet tight deadlines without compromising on quality.
Third, innovation is a key strength. Many manufacturers in China invest in research and development. They continuously improve their technology and processes. This focus on innovation helps them close the gap with global leaders in the industry.
Finally, the vast network of suppliers and partners in China supports these manufacturers. This network ensures a steady supply of materials and components. You gain from this reliability, as it minimizes production delays.
Weaknesses
Despite their strengths, plastic injection molding machine manufacturers in China face certain weaknesses. One major concern is quality consistency. While many manufacturers produce high-quality machines, some struggle to maintain consistent standards. You might encounter variations in product quality, which can affect your operations.
Another challenge is the perception of technology. Although Chinese manufacturers are advancing, some still lag behind European and Japanese counterparts in high-end technology. If you prioritize cutting-edge technology, you may need to carefully evaluate your options.
Intellectual property protection is another issue. Some businesses worry about the security of their designs and innovations. You should take precautions to safeguard your intellectual property when working with manufacturers in China.
Lastly, communication barriers can pose challenges. Language differences and cultural nuances might lead to misunderstandings. Clear communication is essential to ensure your requirements are met accurately.
By understanding these strengths and weaknesses, you can make informed decisions when choosing plastic injection molding machine manufacturers in China. Balancing cost, quality, and technology will help you find the right partner for your needs.
Global Manufacturers
Strengths
Global manufacturers of injection molding machines offer several strengths that you should consider. First, they lead in technology and innovation. Companies from Europe and Japan, in particular, invest heavily in research and development. This focus results in advanced machines with cutting-edge features. You benefit from their commitment to pushing technological boundaries.
Second, global manufacturers prioritize quality. They adhere to strict quality control standards, ensuring consistent and reliable products. When you choose a global manufacturer, you can expect high-quality machines that meet your specifications.
Third, these manufacturers have a strong reputation. Their long-standing presence in the market builds trust and credibility. You gain confidence knowing that you are partnering with a company that has a proven track record.
Finally, global manufacturers often provide excellent customer support. They offer comprehensive training and after-sales services. This support helps you maximize the efficiency and lifespan of your machines.
Weaknesses
Despite their strengths, global manufacturers face certain weaknesses. One major drawback is cost. Their machines often come with a higher price tag. You might find it challenging to balance your budget when considering these options.
Another issue is lead time. Global manufacturers may have longer production and delivery times. If you need machines quickly, this delay could impact your operations.
Additionally, some global manufacturers have limited customization options. They may offer standard models that do not fully meet your unique needs. You might need to compromise on certain features or specifications.
Lastly, navigating international logistics can be complex. Importing machines from global manufacturers involves dealing with customs and shipping regulations. You must be prepared to handle these logistical challenges.
By weighing these strengths and weaknesses, you can make informed decisions about partnering with global manufacturers. Consider your priorities and requirements to find the best fit for your business.
Comparative Analysis
Quality
When you evaluate the quality of injection molding machines, you notice distinct differences between Chinese and global manufacturers. Global manufacturers, particularly those from Europe and Japan, often lead in quality. They adhere to strict quality control standards, ensuring that their machines consistently meet high specifications. You can expect durable and reliable machines from these manufacturers.
In contrast, plastic injection molding machine manufacturers in China have made significant strides in improving quality. Many Chinese manufacturers now produce machines that rival their global counterparts. However, some inconsistencies still exist. You might encounter variations in quality among different Chinese manufacturers. It’s crucial to conduct thorough research and choose reputable companies to ensure you receive a high-quality product.
Cost
Cost is a critical factor when choosing an injection molding machine. Chinese manufacturers typically offer more competitive pricing. Their extensive production capabilities and lower labor costs allow them to produce machines at reduced prices. If you prioritize affordability, Chinese manufacturers present an attractive option.
Global manufacturers, on the other hand, often come with a higher price tag. The advanced technology and stringent quality standards contribute to the increased cost. While you may pay more upfront, the investment can lead to long-term savings through reduced maintenance and higher efficiency.
Technology
Technology plays a vital role in the performance of injection molding machines. Global manufacturers often lead in technological advancements. They invest heavily in research and development, resulting in machines with cutting-edge features. You benefit from their commitment to innovation, which can enhance your production processes.
Chinese manufacturers are rapidly closing the technology gap. Many invest in research and development to improve their offerings. You can find Chinese machines with advanced features, although they may not always match the sophistication of global models. When considering technology, assess your specific needs and determine which manufacturer aligns best with your requirements.
Market Presence
When you examine the market presence of injection molding machine manufacturers, you notice distinct differences between Chinese and global players. Understanding these differences helps you make informed decisions about which manufacturer aligns best with your business goals.
-
Chinese Manufacturers:
Chinese manufacturers have a strong foothold in the global market. Their extensive production capabilities allow them to cater to a wide range of industries. You often find their machines in sectors like automotive, consumer goods, and packaging. The affordability of Chinese machines makes them popular choices for businesses worldwide. This widespread adoption enhances their market presence, making them significant players in the industry.
-
Global Manufacturers:
Global manufacturers, particularly those from Europe and Japan, maintain a robust market presence through their reputation for quality and innovation. You see their machines in high-end applications where precision and advanced technology are crucial. These manufacturers often dominate markets that demand cutting-edge solutions. Their established brand names and long-standing industry experience contribute to their strong market position.
-
Regional Influence:
Chinese manufacturers have a significant influence in Asia and emerging markets. Their competitive pricing and ability to meet large-scale demands make them attractive in these regions. In contrast, global manufacturers have a strong presence in North America and Europe. Their focus on quality and technology appeals to businesses in these areas, where high standards are a priority.
-
Export Strength:
China’s export strength plays a crucial role in its market presence. Many companies choose Chinese manufacturers for their cost advantages and reliable supply chains. This export capability allows Chinese manufacturers to penetrate various international markets effectively. Global manufacturers also export extensively, but their higher costs may limit their reach in price-sensitive markets.
By understanding the market presence of both Chinese and global manufacturers, you can better assess which option suits your business needs. Consider factors like regional influence, export capabilities, and industry demands when making your decision.
Case Studies
Companies Choosing Chinese Manufacturers
-
Cost Efficiency:
Many companies opt for Chinese manufacturers due to cost efficiency. You find that businesses with tight budgets benefit from the competitive pricing offered by Chinese manufacturers. For instance, a mid-sized toy company in the United States chose a Chinese manufacturer to produce its plastic components. The decision resulted in significant cost savings, allowing the company to allocate more resources to marketing and distribution.
-
Scalability:
Chinese manufacturers excel in handling large orders. A European automotive parts supplier selected a Chinese manufacturer to meet its high production demands. The supplier needed a partner capable of delivering large quantities within a short timeframe. The Chinese manufacturer met these requirements, ensuring timely delivery without compromising quality.
-
Innovation and Adaptability:
Some companies appreciate the innovation and adaptability of Chinese manufacturers. A startup in the consumer electronics sector partnered with a Chinese manufacturer to develop a new product line. The manufacturer provided valuable insights and suggestions, enhancing the product’s design and functionality. This collaboration led to a successful product launch and increased market share.
-
Strong Supply Chain:
The robust supply chain network in China attracts companies seeking reliable production. A global packaging company chose a Chinese manufacturer for its injection molding needs. The manufacturer leveraged its extensive network of suppliers to ensure a steady flow of materials. This reliability minimized production delays and maintained the company’s competitive edge.
Companies Choosing Global Manufacturers
-
Quality Assurance:
Companies prioritize quality often choose global manufacturers. A medical device company in Canada selected a European manufacturer for its injection molding machines. The company valued the strict quality control standards and advanced technology offered by the manufacturer. This choice ensured the production of high-quality medical devices that met regulatory requirements.
-
Advanced Technology:
Businesses seeking cutting-edge technology often turn to global manufacturers. A Japanese electronics giant partnered with a global manufacturer known for its innovative solutions. The manufacturer provided machines with advanced features, enhancing the company’s production capabilities. This partnership allowed the electronics giant to maintain its position as an industry leader.
-
Reputation and Trust:
The reputation and trust associated with global manufacturers attract many companies. A luxury automotive brand in Germany chose a global manufacturer for its injection molding needs. The brand valued the manufacturer’s long-standing presence and proven track record. This decision reinforced the brand’s commitment to quality and excellence.
-
Comprehensive Support:
Global manufacturers often offer comprehensive support, which appeals to companies seeking reliable partnerships. An American aerospace company partnered with a global manufacturer for its injection molding machines. The manufacturer provided extensive training and after-sales services, ensuring optimal machine performance. This support helped the aerospace company maximize efficiency and reduce downtime.
By examining these case studies, you gain insights into the factors influencing companies’ choices between Chinese and global manufacturers. Consider your priorities, such as cost, quality, and technology, to make informed decisions that align with your business goals.
You now understand the key differences between Chinese and global injection molding machine manufacturers. Chinese manufacturers offer cost-effective solutions and scalability, while global manufacturers excel in quality and technology. To choose the right partner, consider your business needs. If cost is a priority, Chinese manufacturers may suit you. For advanced technology and quality, global manufacturers might be better. Think about both short-term savings and long-term benefits. Your decision will impact your production efficiency and market competitiveness.
Post time: Nov-22-2024