Key Takeaways
- Choosing a servo motor injection molding machine can significantly enhance manufacturing efficiency and reduce energy costs by up to 60%.
- Fully-electric machines offer the highest precision and energy savings, making them ideal for high-precision applications like medical devices.
- Hybrid machines provide versatility by combining the strengths of electric and hydraulic systems, suitable for applications requiring high clamping forces.
- Regular maintenance is crucial for all machine types, but servo motor machines generally require less upkeep, leading to lower long-term costs.
- Consider the total cost of ownership, including energy savings and maintenance, rather than just the initial investment when selecting a machine.
- Testing machines through trial runs is essential to ensure they meet your production needs in terms of precision, cycle time, and material compatibility.
- Researching reputable manufacturers and their support services can greatly enhance your investment’s value and ensure smooth operations.
Types of Servo Motor Injection Molding Machines
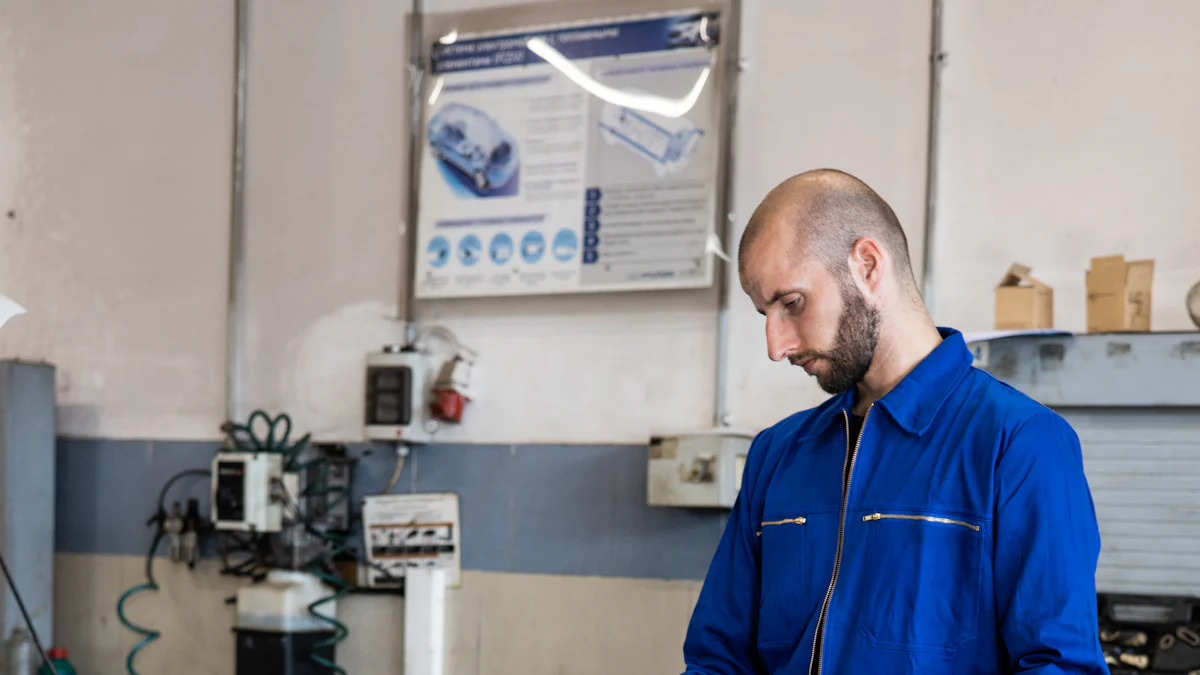
Fully-Electric Machines
Fully-electric machines rely entirely on electric servo motors to manage all operational movements. These machines excel in precision, speed, and energy efficiency. I have observed that they consume significantly less energy compared to hydraulic systems, making them a top choice for manufacturers aiming to reduce operational costs. Additionally, they operate with minimal noise and require less lubrication, which translates to lower maintenance needs.
One standout feature of fully-electric machines is their ability to recover kinetic energy during operation. This energy recovery system enhances overall efficiency and contributes to long-term savings. For instance, Crate450S Servo Motor Plastic Injection Molding Machine utilize servo motors for real-time control and high-speed operations. These machines deliver exceptional accuracy while consuming less energy, making them ideal for high-precision production environments.
Hybrid Machines
Hybrid machines combine the best of both worlds by integrating electric servo motors with traditional hydraulic systems. This blend offers a balance between energy efficiency and power. I find these machines particularly useful for applications requiring high clamping forces, as the hydraulic components provide the necessary strength while the servo motors ensure precision.
Manufacturers often choose hybrid machines when they need versatility. These machines can handle a wide range of materials and mold complexities. They also offer improved energy savings compared to fully hydraulic systems, though not as much as fully-electric models. Their adaptability makes them a practical choice for diverse production needs.
Servo Hydraulic Machines
Servo hydraulic machines represent a modern evolution of traditional hydraulic systems. They use servo motors to drive the hydraulic pumps, which significantly reduces energy consumption. Unlike older hydraulic models, these machines only consume energy when needed, leading to operational cost savings.
I have noticed that servo hydraulic machines strike a good balance between performance and affordability. They deliver high power and torque, making them suitable for heavy-duty applications. Additionally, their energy efficiency and reduced noise levels make them an attractive option for manufacturers looking to upgrade from conventional hydraulic systems without a substantial increase in initial investment.
Traditional Hydraulic Machines
Traditional hydraulic machines rely on hydraulic systems to power their operations. These machines have been a cornerstone in the injection molding industry for decades. I often see manufacturers choosing them for their robust performance and ability to handle high-pressure applications. Their design ensures they can manage heavy-duty tasks, making them suitable for large-scale production.
One key advantage of traditional hydraulic machines lies in their affordability. They typically come with a lower initial investment compared to fully-electric or hybrid models. This cost-effectiveness appeals to businesses with tight budgets or those just starting in the injection molding industry. However, I always advise considering long-term operational costs when evaluating these machines.
In terms of maintenance, traditional hydraulic machines require regular oil changes and system checks to ensure optimal performance. Neglecting these tasks can lead to increased wear and tear, which may result in higher repair costs over time. I recommend keeping a strict maintenance schedule to avoid unexpected downtime.
While traditional hydraulic machines deliver reliable power, they consume more energy than their modern counterparts. This higher energy consumption can lead to increased operational costs, especially for businesses running multiple machines. Additionally, they tend to generate more noise during operation, which might not be ideal for all manufacturing environments.
Despite these challenges, traditional hydraulic machines remain a viable option for manufacturers prioritizing upfront affordability and proven reliability. For businesses focusing on heavy-duty applications, these machines continue to offer dependable performance. However, I encourage buyers to weigh the trade-offs between initial cost savings and long-term efficiency when making their decision.
Energy Efficiency and Performance
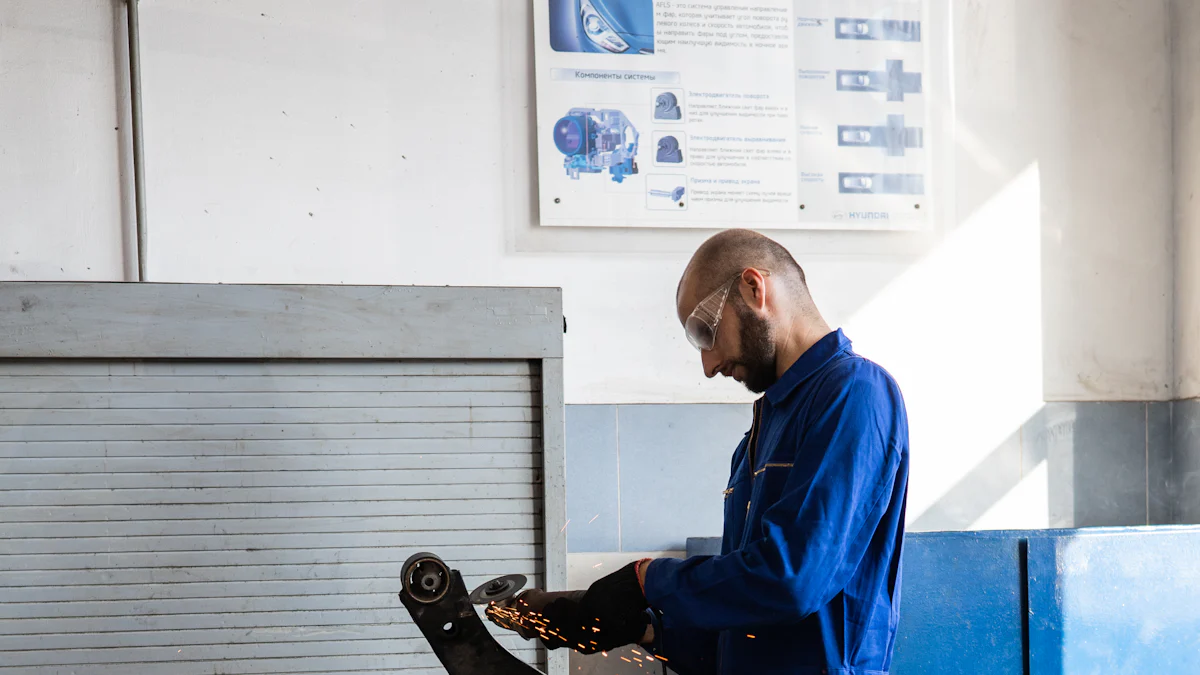
Comparing Energy Consumption
Energy consumption plays a critical role in the operational costs of injection molding machines. I have observed that servo motor-driven systems consume energy only when needed, unlike traditional hydraulic machines that run continuously. This on-demand energy usage can reduce electricity costs by up to 60%, making servo motor machines a cost-effective choice for manufacturers.
Fully-electric machines lead the way in energy efficiency. They recover kinetic energy during operation, which further minimizes power usage. Hybrid and servo hydraulic machines also offer significant savings compared to traditional hydraulic systems. For example, hybrid machines combine the precision of servo motors with the power of hydraulics, striking a balance between energy efficiency and performance. Traditional hydraulic machines, while robust, consume more energy due to their constant operation. This higher energy demand often results in increased utility bills, especially in facilities running multiple machines.
Precision and Repeatability
Precision and repeatability are essential for maintaining product quality in injection molding. Servo motor machines excel in this area. I have seen how their advanced control systems ensure consistent movements, leading to uniform product dimensions. Fully-electric machines, in particular, deliver exceptional accuracy, making them ideal for high-precision applications like medical devices or electronics.
Hybrid and servo hydraulic machines also provide reliable precision. The integration of servo motors allows for better control over the molding process, reducing material waste and improving overall efficiency. Traditional hydraulic machines, while powerful, may struggle to match the precision of their modern counterparts. Their reliance on mechanical components can lead to slight variations in product quality, especially during long production runs.
Noise Levels and Environmental Impact
Noise levels and environmental impact are often overlooked but remain crucial factors in machine selection. Servo motor machines operate quietly compared to traditional hydraulic systems. I have noticed that fully-electric machines produce minimal noise, creating a more comfortable working environment. This feature is particularly beneficial in facilities where multiple machines run simultaneously.
Hybrid and servo hydraulic machines also offer reduced noise levels. The servo motors drive the hydraulic pumps efficiently, minimizing unnecessary vibrations. Traditional hydraulic machines, however, generate more noise due to their constant operation and mechanical components. This can be disruptive in certain manufacturing settings.
From an environmental perspective, servo motor machines stand out. Their energy-efficient design reduces carbon emissions, aligning with sustainability goals. Fully-electric machines, with their ability to recover kinetic energy, further enhance their eco-friendly credentials. Traditional hydraulic machines, while reliable, consume more energy and produce higher emissions, making them less environmentally friendly.
“The development of hydraulic systems dates back to ancient civilizations like the Egyptians and Greeks, who harnessed water power for tasks like irrigation and lifting heavy objects.” This historical foundation highlights the evolution of hydraulic technology, culminating in today’s advanced servo motor systems. By choosing energy-efficient machines, manufacturers not only reduce costs but also contribute to a more sustainable future.
Servo Motor for Injection Molding Machine Price and ROI
Initial Investment Costs
The initial investment cost is a critical factor when selecting a servo motor injection molding machine. I have noticed that these machines often require a higher upfront expenditure compared to traditional hydraulic systems. This cost difference stems from the advanced technology embedded in servo motors, which ensures precision, energy efficiency, and reliability. Fully-electric machines, for instance, tend to have the highest initial price due to their cutting-edge design and superior performance.
However, I always emphasize that this initial cost should not deter buyers. The servo motor for injection molding machine price reflects the long-term value these machines provide. Unlike traditional hydraulic machines, servo motor-driven systems consume energy only when needed. This feature alone can lead to substantial savings over time, justifying the initial investment. Additionally, the reduced maintenance requirements of servo motor machines further contribute to cost-effectiveness in the long run.
Long-Term Savings
When evaluating the total cost of ownership, long-term savings play a pivotal role. I have observed that servo motor machines significantly reduce operational expenses. Their energy-efficient design minimizes electricity consumption, with savings ranging from 40% to 60% compared to traditional hydraulic systems. For example, hybrid machines, which combine servo motors with hydraulic components, strike an excellent balance between energy efficiency and performance. These machines consume less power while maintaining the strength needed for demanding applications.
Moreover, the precision of servo motor systems reduces material waste during production. This accuracy ensures consistent product quality, which minimizes defects and rework costs. Fully-electric machines, in particular, excel in this area, making them ideal for industries requiring high precision, such as medical or electronics manufacturing. Over time, these savings can offset the higher servo motor for injection molding machine price, delivering a strong return on investment.
Maintenance costs also decrease with servo motor machines. Traditional hydraulic systems often require frequent oil changes and component replacements, which can add up over time. In contrast, servo motor-driven machines demand less upkeep, further enhancing their cost-effectiveness. I always recommend considering these long-term benefits when assessing the overall value of an injection molding machine.
Market Trends and ROI
The market for servo motor injection molding machines continues to evolve, driven by advancements in technology and growing demand for energy-efficient solutions. I have noticed a clear trend toward fully-electric and hybrid machines, as manufacturers prioritize sustainability and cost savings. These machines align with global efforts to reduce carbon emissions and promote eco-friendly practices.
Investing in a servo motor injection molding machine offers a compelling return on investment (ROI). The combination of energy savings, reduced maintenance costs, and improved production efficiency ensures that these machines pay for themselves over time. For instance, businesses that switch from traditional hydraulic systems to servo motor-driven machines often report significant reductions in operational expenses within the first few years.
Additionally, the rising demand for high-quality, precision-molded products enhances the value of servo motor machines. Their ability to deliver consistent results positions manufacturers to meet market expectations and secure long-term contracts. This reliability, coupled with the cost savings, makes the higher servo motor for injection molding machine price a worthwhile investment.
“Energy-efficient technologies are not just a trend but a necessity in modern manufacturing.” This statement underscores the importance of adopting servo motor systems to stay competitive in today’s market. By choosing machines that balance cost, performance, and sustainability, manufacturers can achieve both financial and operational success.
Maintenance and Complexity
Service Requirements
Proper maintenance ensures the longevity and efficiency of servo motor injection molding machines. I have observed that these machines demand less frequent servicing compared to traditional hydraulic systems. The advanced design of servo motors minimizes wear and tear, reducing the need for constant repairs. Fully-electric machines, for instance, operate without hydraulic oil, which eliminates the need for oil-related maintenance tasks. This simplicity translates into lower service costs and fewer interruptions in production.
Hybrid and servo hydraulic machines also benefit from reduced service requirements. The integration of servo motors enhances the reliability of these systems, as they consume energy only when needed. This on-demand operation reduces strain on components, extending their lifespan. Traditional hydraulic machines, however, require more frequent servicing due to their continuous operation and reliance on mechanical parts. Regular inspections and timely repairs are essential to prevent unexpected breakdowns.
I always recommend scheduling routine maintenance checks to identify potential issues early. Preventive maintenance not only avoids costly repairs but also ensures consistent machine performance. Partnering with manufacturers that offer reliable technical support can further simplify the servicing process.
Oil Maintenance and Cleanliness
Oil maintenance plays a critical role in the performance of injection molding machines, particularly for those with hydraulic components. Servo hydraulic and hybrid machines require less oil compared to traditional hydraulic systems. The servo motor’s ability to drive pumps efficiently reduces the overall oil usage, which lowers maintenance costs. Additionally, these machines consume energy only when needed, which minimizes oil contamination and degradation.
Traditional hydraulic machines, on the other hand, demand regular oil changes to maintain optimal performance. I have seen how neglecting oil cleanliness can lead to increased wear on components, resulting in higher repair costs. Contaminated oil can also compromise the precision of the molding process, affecting product quality. For this reason, I always advise maintaining a strict oil maintenance schedule for hydraulic systems.
Fully-electric machines eliminate the need for hydraulic oil altogether. This feature not only simplifies maintenance but also reduces environmental impact. By choosing machines with minimal oil requirements, manufacturers can achieve cleaner operations and lower maintenance expenses.
Machine Complexity
The complexity of a machine directly impacts its usability and maintenance needs. Fully-electric machines feature a simpler mechanical design compared to hydraulic systems. I find this simplicity advantageous for operators, as it reduces the learning curve and streamlines troubleshooting. The absence of hydraulic components also minimizes the risk of leaks and mechanical failures, making these machines easier to manage.
Hybrid and servo hydraulic machines strike a balance between complexity and functionality. While they incorporate hydraulic elements, the integration of servo motors simplifies their operation. These machines offer the power of hydraulics with the precision and efficiency of servo technology. However, their dual-system design may require specialized knowledge for maintenance and repairs.
Traditional hydraulic machines, with their robust construction, often involve more complex maintenance procedures. Their reliance on multiple mechanical components increases the likelihood of wear and tear. I have noticed that operators need extensive training to handle these systems effectively. While their durability remains a strength, their complexity can pose challenges for less experienced teams.
When selecting a machine, I always recommend considering the skill level of the maintenance team. Opting for a machine with a manageable level of complexity ensures smoother operations and reduces downtime. Manufacturers offering comprehensive training and support can further enhance the usability of these machines.
Practical Tips for Buyers
Assessing Production Needs
Understanding production needs is the first step in selecting the right injection molding machine. I always recommend evaluating the type of products you plan to manufacture. Consider factors like material type, mold complexity, and production volume. For instance, high-precision industries such as medical devices or electronics often require fully-electric machines due to their accuracy and repeatability. On the other hand, hybrid or servo hydraulic machines may suit applications demanding higher clamping forces or versatility.
Cycle time is another critical aspect. Faster cycle times can boost productivity, but they also demand machines with advanced servo motor systems. These motors ensure consistent performance even under high-speed operations. Additionally, assess the size and weight of the molds you will use. Machines with insufficient clamping force or platen size may limit your production capabilities. By aligning machine specifications with production requirements, you can avoid unnecessary costs and inefficiencies.
Budget and Cost Considerations
Budget plays a pivotal role in the decision-making process. I often advise buyers to look beyond the initial investment cost and consider the total cost of ownership. While the servo motor for injection molding machine price may seem higher upfront, these machines offer significant long-term savings. Their energy-efficient design reduces electricity consumption, and their precision minimizes material waste. Fully-electric machines, for example, deliver exceptional energy savings and lower maintenance costs, making them a worthwhile investment for high-precision applications.
Hybrid and servo hydraulic machines provide a balance between affordability and performance. They consume less energy than traditional hydraulic systems while offering robust power for demanding tasks. Traditional hydraulic machines, though more affordable initially, often incur higher operational costs due to their continuous energy consumption and frequent maintenance needs. I always recommend calculating potential savings over the machine’s lifespan to determine its true value.
Financing options can also ease the financial burden. Many manufacturers and suppliers offer flexible payment plans or leasing options. Exploring these alternatives can help you acquire a high-quality machine without straining your budget. Remember, investing in a reliable machine ensures consistent production and reduces downtime, ultimately enhancing profitability.
Researching Manufacturers and Suppliers
Choosing the right manufacturer or supplier is as important as selecting the machine itself. I always emphasize the importance of researching the reputation and reliability of potential vendors. Look for manufacturers with a proven track record in producing high-quality servo motor injection molding machines. Customer reviews and testimonials can provide valuable insights into their performance and after-sales support.
Technical support and maintenance services are crucial. Reliable manufacturers often offer comprehensive training programs and responsive customer service. These services ensure smooth operations and quick resolution of any issues. Additionally, inquire about warranty terms and spare parts availability. A strong warranty reflects the manufacturer’s confidence in their product’s durability and performance.
Visiting trade shows or industry events can also be beneficial. These platforms allow you to interact with multiple manufacturers, compare machines, and even witness live demonstrations. Testing machines before purchase is another effective way to evaluate their performance and compatibility with your production needs. By partnering with a reputable manufacturer, you can secure a machine that aligns with your operational goals and delivers long-term value.
Testing and Trial Runs
Testing and trial runs play a crucial role in selecting the right servo motor injection molding machine. I always recommend conducting thorough tests to evaluate the machine’s performance under real-world conditions. This step ensures that the machine aligns with your production requirements and delivers consistent results.
When testing a machine, I focus on several key aspects:
-
Precision and Repeatability
I assess the machine’s ability to produce uniform products across multiple cycles. Servo motor machines excel in precision, but it is essential to verify this through trial runs. Consistent dimensions and minimal defects indicate reliable performance. Fully-electric machines often stand out in this area due to their advanced control systems.
-
Energy Efficiency
During the trial, I monitor the machine’s energy consumption. Machines powered by servo motors consume energy only when needed, which reduces operational costs. Comparing energy usage during high-speed operations provides valuable insights into long-term savings. Hybrid and servo hydraulic machines typically strike a balance between energy efficiency and power.
-
Cycle Time
Faster cycle times can enhance productivity. I measure the time taken for each production cycle to ensure the machine meets the required speed without compromising quality. Servo motor systems often deliver faster and more efficient cycles, making them ideal for high-volume production.
-
Noise Levels
Noise can impact the working environment. I observe the machine’s noise levels during operation. Fully-electric machines usually operate quietly, creating a more comfortable workspace. Reduced noise also reflects the machine’s efficiency and advanced design.
-
Compatibility with Materials and Molds
I test the machine with the specific materials and molds intended for production. This step confirms that the machine can handle the complexity of the molds and the properties of the materials. Machines with insufficient clamping force or platen size may struggle with certain applications.
“Testing ensures that the machine performs as expected and meets the unique demands of your production process.” This approach minimizes risks and helps avoid costly mistakes.
Additionally, I recommend collaborating with manufacturers during the trial phase. Many manufacturers offer on-site demonstrations or allow buyers to test machines at their facilities. This hands-on experience provides an opportunity to evaluate the machine’s features and functionality. It also allows you to ask questions and gain insights from the manufacturer’s technical team.
Finally, I suggest documenting the results of each trial run. Keeping detailed records helps compare different machines and make an informed decision. By prioritizing testing and trial runs, you can confidently invest in a servo motor injection molding machine that delivers long-term value and aligns with your operational goals.
Choosing the right servo motor injection molding machine requires careful consideration of several factors. I always emphasize evaluating machine types, energy efficiency, costs, maintenance needs, and production goals. Fully-electric machines, for instance, deliver unmatched energy savings, with consumption up to 70% lower than hydraulic presses. Aligning the machine choice with operational objectives ensures maximum efficiency and ROI. Thorough research and expert consultation are essential steps. By understanding the servo motor for injection molding machine price and its long-term benefits, manufacturers can make informed decisions that drive success.
Post time: Nov-23-2024