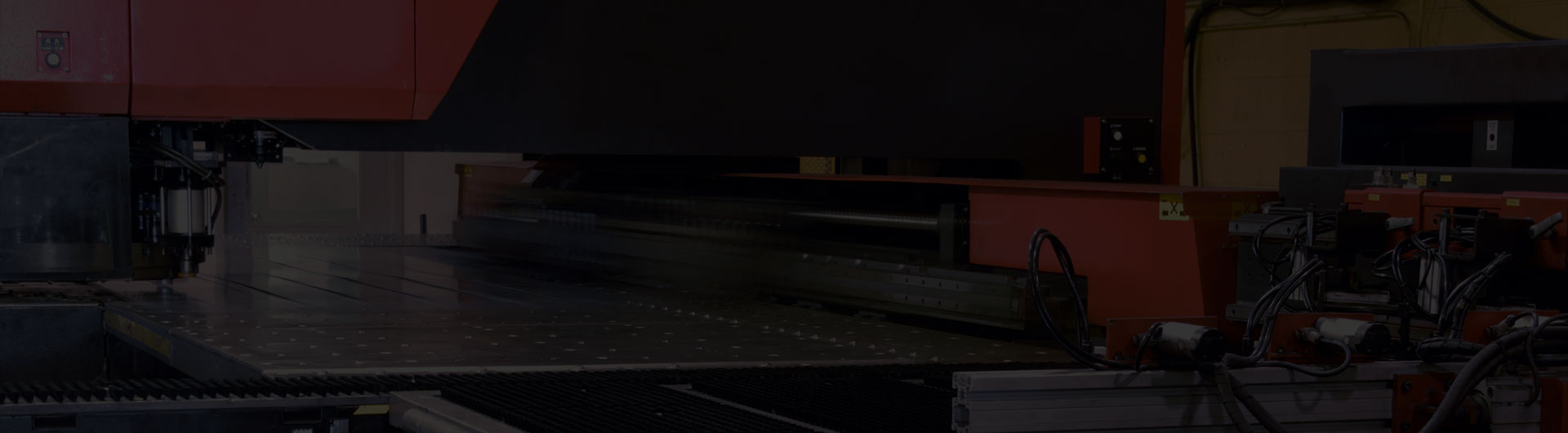
I’ve seen many machines in the manufacturing world, but the PET360/2500 S6 stands out. This Plastic Injection Molding Machine changes the game with its unmatched efficiency and precision. It’s built for PET bottle production, delivering consistent results every time. The energy-saving features caught my attention right away. They don’t just cut costs; they also support eco-friendly practices. Its innovative design makes it versatile, handling various production needs with ease. If you’re looking for a reliable solution that combines performance and cost-effectiveness, this machine is a clear winner.
Key Takeaways
- The PET360/2500 S6 offers unmatched efficiency and precision, making it ideal for high-quality PET bottle production.
- Energy-saving features, including advanced servo motor technology, can reduce energy consumption by up to 50%, lowering operational costs and supporting eco-friendly practices.
- Its specialized PET screw and barrel enhance performance by improving charge speed and reducing material degradation, resulting in better bottle transparency.
- The machine’s variable pump technology saves 25% to 45% more energy, ensuring smoother operations and minimizing production issues.
- A fully enclosed clamping unit ensures consistent pressure and quality, reducing defects and maintaining a clean operating environment.
- The versatile design allows for quick adjustments between different bottle sizes and applications, making it a smart investment for manufacturers facing changing market demands.
- With long-term durability and minimal maintenance requirements, the PET360/2500 S6 provides a high return on investment, making it a cost-effective solution for various industries.
Key Features of the PET360/2500 S6 Plastic Injection Molding Machine
Specialized PET Screw and Barrel for Enhanced Performance
I’ve worked with many machines, but the PET360/2500 S6 takes performance to another level. Its specially designed PET screw and barrel caught my attention right away. This feature boosts charge speed and injection weight, which means faster production without compromising quality. It also reduces plasticizing temperature, so material degradation becomes less of a concern. I’ve noticed how this directly improves bottle transparency and contraction. If you’re aiming for high-quality PET products, this machine delivers every time.
Advanced Servo Motor Technology for Energy Efficiency
Energy efficiency matters more than ever, and the PET360/2500 S6 doesn’t disappoint. Its advanced servo motor technology saves up to 50% more energy compared to traditional systems. I’ve seen how this impacts operational costs—it’s a game-changer. The motor adjusts its speed based on the workload, so energy isn’t wasted. This not only lowers expenses but also supports eco-friendly manufacturing. For me, this balance between performance and sustainability makes it stand out in the world of plastic injection molding machines.
Variable Pump Technology for Reduced Operational Costs
The variable pump technology in this machine is another feature I can’t overlook. It saves between 25% to 45% more energy than fixed pumps. This means lower electricity bills and reduced overall costs. I’ve noticed how this technology also ensures smoother operations. By maintaining consistent pressure, it minimizes issues like overflow burrs, which can occur with faster flow rates. This level of precision keeps production efficient and hassle-free. If you’re looking to cut costs while maintaining quality, this feature alone makes the PET360/2500 S6 worth considering.
Fully Enclosed Clamping Unit for Precision and Quality
The fully enclosed clamping unit on the PET360/2500 S6 impressed me right away. It’s not just about keeping things neat; it’s about delivering precision and maintaining quality. I’ve seen how this design ensures consistent pressure during the molding process. This consistency eliminates common issues like overflow burrs, which can ruin the final product. The enclosed setup also keeps the mold temperature stable. Stable temperatures mean smoother material flow, which directly impacts the quality of the PET bottles.
What I love most is how this feature minimizes external interference. Dust and debris don’t stand a chance, so the machine operates in a clean environment. This cleanliness translates to fewer defects and higher-quality output. I’ve noticed how this setup also reduces noise during operation, making the workspace more comfortable. If you’re aiming for precision and reliability, this clamping unit delivers every time.
Versatile Design for Various Bottle Sizes and Applications
Versatility is key in manufacturing, and the PET360/2500 S6 doesn’t disappoint. Its design adapts to different bottle sizes with ease. Whether you’re producing small bottles for beverages or larger ones for industrial use, this machine handles it all. I’ve worked with machines that struggle to switch between sizes, but this one makes it seamless. Adjustments are quick, so downtime stays minimal.
The machine’s adaptability goes beyond bottle sizes. It works well for various applications, from food packaging to medical supplies. I’ve seen how manufacturers use it to meet changing market demands without needing new equipment. This flexibility saves time and money. For me, this versatility makes the PET360/2500 S6 a smart investment for any production line.
Performance and Efficiency of the PET360/2500 S6
Faster Cycle Times and Increased Production Capacity
I’ve seen how the PET360/2500 S6 transforms production speed. Its design focuses on faster cycle times, which means more bottles in less time. This machine doesn’t just work quickly; it works efficiently. I’ve noticed how it maintains quality even when the pace picks up. The faster cycles directly boost production capacity. For manufacturers, this means meeting high demand without delays. I’ve worked with machines that slow down under pressure, but this one keeps going strong. It’s built to handle large-scale operations without breaking a sweat.
Improved Bottle Transparency and Reduced Material Degradation
Transparency matters in PET bottles, and this machine delivers. I’ve seen how the PET360/2500 S6 enhances bottle clarity. Its specialized screw and barrel reduce plasticizing temperature, which minimizes material degradation. This process keeps the material pure, resulting in bottles with better transparency. I’ve noticed how this also improves the overall appearance of the final product. Manufacturers aiming for premium-quality bottles will appreciate this feature. It’s not just about looks; it’s about maintaining the integrity of the material. This machine ensures every bottle meets high standards.
Synchronized Holding Pressure System for Higher Output
The synchronized holding pressure system is a game-changer. I’ve watched how it increases output by up to 25%. This system ensures consistent pressure during the molding process, which leads to uniform results. I’ve noticed how this reduces defects and waste. For manufacturers, this means more usable products and less material loss. The system also supports higher production rates without compromising quality. I’ve worked with machines that struggle to balance speed and precision, but the PET360/2500 S6 handles both effortlessly. It’s a reliable choice for anyone looking to maximize efficiency.
Consistent Quality with Advanced Temperature Control
I’ve always believed that temperature control plays a huge role in maintaining product quality, and the PET360/2500 S6 proves me right. This machine’s advanced temperature control system ensures every bottle meets the highest standards. I’ve seen how it keeps the material flow steady, which directly impacts the consistency of the final product. When the temperature stays stable, the results speak for themselves—smooth, flawless bottles every time.
What stands out to me is how this system prevents overheating. Overheating can degrade materials, but this machine keeps that in check. I’ve noticed how it maintains the perfect balance, so the material stays pure. This purity translates into better transparency and durability for the bottles. It’s not just about avoiding defects; it’s about creating products that look and perform their best.
Another thing I love is how this feature reduces waste. I’ve worked with machines where inconsistent temperatures led to rejected batches. That’s not the case here. The PET360/2500 S6 minimizes errors, so you get more usable products. For manufacturers, this means saving time and resources. I’ve seen firsthand how this boosts efficiency without cutting corners on quality.
The machine’s precision amazes me. It adjusts the temperature in real-time, responding to changes during the process. This adaptability ensures the material stays within the ideal range. I’ve watched how this eliminates common issues like uneven thickness or weak spots in the bottles. If you’re aiming for consistent results, this feature delivers every single time.
For me, the advanced temperature control system isn’t just a technical detail—it’s a game-changer. It ensures reliability, reduces waste, and enhances the overall quality of the output. I’ve worked with many machines, but this one sets a new standard. If you care about precision and consistency, this is the kind of technology you need in your production line.
Cost-Effectiveness of the PET360/2500 S6
Energy Savings of Up to 50% with Servo Motor Technology
I’ve always believed that energy efficiency is a cornerstone of cost-effectiveness, and the PET360/2500 S6 proves this point. Its servo motor technology saves up to 50% more energy compared to traditional systems. This isn’t just a claim; I’ve seen it in action. The motor adjusts its speed based on the workload, ensuring no energy goes to waste. This smart design lowers electricity bills significantly, which directly impacts operational costs.
What stands out to me is how this technology aligns with today’s eco-conscious manufacturing needs. By consuming less energy, the machine reduces its carbon footprint. This makes it a win-win for both businesses and the environment. I’ve noticed how manufacturers using this machine can meet sustainability goals without sacrificing performance. For anyone looking to cut costs while staying green, this feature is a game-changer.
Long-Term Durability and Minimal Maintenance Requirements
Durability matters in manufacturing, and the PET360/2500 S6 delivers on this front. I’ve worked with machines that require constant maintenance, but this one stands apart. Its robust design ensures long-term reliability, reducing the need for frequent repairs. This durability translates into fewer interruptions, which keeps production running smoothly.
What I appreciate most is how easy it is to maintain. The machine’s components are built to last, so wear and tear happen at a slower rate. I’ve seen how this minimizes downtime, saving both time and money. Regular maintenance becomes less of a hassle, allowing manufacturers to focus on what matters—producing high-quality PET bottles. For me, this combination of durability and low maintenance makes the PET360/2500 S6 a smart investment.
High Return on Investment Through Reduced Downtime
Downtime can be a costly problem, but the PET360/2500 S6 tackles it head-on. I’ve noticed how its efficient design reduces the chances of unexpected breakdowns. This reliability keeps production lines running, which means fewer delays and higher output. For manufacturers, this directly translates into a higher return on investment.
The machine’s advanced features, like its synchronized holding pressure system and precise temperature control, also play a role in minimizing downtime. These technologies ensure consistent performance, so there’s no need to pause operations for adjustments or fixes. I’ve seen how this boosts productivity while maintaining quality. If you’re aiming to maximize profits, this machine makes it possible by keeping downtime to a minimum.
In my experience, the PET360/2500 S6 isn’t just a Plastic Injection Molding Machine—it’s a cost-effective solution that delivers long-term value. Its energy efficiency, durability, and ability to reduce downtime make it a standout choice for any manufacturer.
Competitive Pricing for Advanced Manufacturing Solutions
I’ve always believed that advanced technology doesn’t have to come with an overwhelming price tag, and the PET360/2500 S6 proves this point perfectly. This machine offers cutting-edge features at a price that makes sense for manufacturers. It’s rare to find a solution that combines high performance, energy efficiency, and affordability, but this one checks all the boxes.
What stands out to me is how the PET360/2500 S6 delivers long-term value. Its energy-saving capabilities alone make it a cost-effective choice. With servo motor technology reducing energy consumption by up to 50%, operational costs drop significantly. Over time, these savings add up, making the initial investment worthwhile. I’ve seen how manufacturers using this machine can allocate those savings to other areas of their business, boosting overall profitability.
Another factor that makes this machine a smart financial choice is its ability to shorten production cycles. The advanced cooling system ensures faster solidification of plastic parts, which reduces cycle times. I’ve noticed how this directly impacts productivity. By completing more cycles in less time, manufacturers can increase output without needing additional resources. This efficiency translates into higher revenue potential, making the PET360/2500 S6 a competitive option in the market.
“Experience shows that a savings potential of 10-40% can be attained in the injection molding process through optimized mold cooling.”
This quote resonates with me because I’ve seen firsthand how precise temperature control can improve economic efficiency. The PET360/2500 S6 excels in this area, ensuring consistent cooling and reducing the risk of defects. Fewer defects mean less waste, which further lowers production costs. For manufacturers, this reliability eliminates the need for costly rework or material loss, adding another layer of financial benefit.
The versatility of this machine also plays a role in its cost-effectiveness. Its ability to handle various bottle sizes and applications means manufacturers don’t need to invest in multiple machines. I’ve worked with companies that struggled to adapt to changing market demands because their equipment lacked flexibility. The PET360/2500 S6 solves this problem, offering a one-stop solution that saves money and simplifies operations.
In my experience, competitive pricing isn’t just about the upfront cost—it’s about the overall value a machine brings to the table. The PET360/2500 S6 delivers on all fronts, making it an excellent choice for manufacturers looking to balance quality, efficiency, and affordability. If you’re searching for a machine that offers advanced manufacturing solutions without breaking the bank, this one stands out as a clear winner.
Applications of the PET360/2500 S6 Plastic Injection Molding Machine
PET Bottle Manufacturing for the Packaging Industry
I’ve seen how the PET360/2500 S6 transforms PET bottle production. This machine excels in creating bottles with exceptional clarity and durability. Its advanced temperature control system ensures consistent cooling, which directly impacts the quality of the final product. I’ve noticed how this precision reduces internal stresses in the material, resulting in bottles that maintain their shape and strength over time.
The versatility of this machine makes it a favorite in the packaging industry. Whether it’s small beverage bottles or larger containers for industrial use, the PET360/2500 S6 handles it all. I’ve worked with manufacturers who appreciate how quickly it adapts to different mold sizes. This flexibility minimizes downtime and keeps production lines running smoothly. For anyone in the packaging sector, this machine is a game-changer.
“Proper mold temperature control helps in achieving consistent part quality and reducing cycle times.”
This insight resonates with me because I’ve seen firsthand how precise temperature management enhances efficiency. The PET360/2500 S6 ensures even cooling throughout the mold, which prevents defects like uneven shrinkage. This reliability makes it an ideal choice for high-volume bottle production.
Automotive Components and Precision Parts Production
The automotive industry demands precision, and the PET360/2500 S6 delivers. I’ve observed how its synchronized holding pressure system ensures uniformity in every part it produces. This consistency is crucial for components like gears, housings, and other precision parts. The machine’s ability to maintain tight tolerances sets it apart from others I’ve worked with.
What stands out to me is how the advanced servo motor technology supports energy-efficient production. Automotive manufacturers often face high operational costs, but this machine helps reduce those expenses. I’ve seen how its energy-saving features align with the industry’s push for sustainable practices. By consuming less energy, it not only lowers costs but also supports eco-friendly manufacturing.
The PET360/2500 S6 also excels in handling complex designs. I’ve noticed how its precise temperature control prevents material degradation, ensuring parts meet strict quality standards. For manufacturers aiming to produce reliable and durable automotive components, this machine is a perfect fit.
Consumer Goods and Electronics Manufacturing
I’ve always believed that versatility is key in consumer goods production, and the PET360/2500 S6 proves me right. This machine adapts effortlessly to a wide range of applications, from household items to electronic casings. I’ve seen how its fully enclosed clamping unit ensures precision, which is critical for products with intricate designs.
The machine’s ability to maintain consistent mold temperatures plays a big role here. I’ve noticed how this feature prevents defects like warping or uneven surfaces. For electronics, where precision is non-negotiable, this level of control makes all the difference. The PET360/2500 S6 ensures every product meets the highest standards of quality and durability.
What I find most impressive is how this machine supports rapid production without compromising quality. Its faster cycle times allow manufacturers to meet tight deadlines while maintaining consistency. I’ve worked with companies that rely on this efficiency to stay competitive in fast-paced markets. For anyone in the consumer goods or electronics sectors, the PET360/2500 S6 offers unmatched reliability and performance.
Medical and Healthcare Equipment Production
I’ve seen how the PET360/2500 S6 excels in producing medical and healthcare equipment. Precision is critical in this field, and this machine delivers it flawlessly. Its advanced temperature control system ensures consistent mold temperatures, which directly impacts the quality of the final product. I’ve noticed how this precision reduces defects, making it ideal for manufacturing items like syringes, vials, and other medical-grade components.
What stands out to me is how the machine prevents material degradation. The specialized screw and barrel design maintain the integrity of the plastic, ensuring the final products meet strict healthcare standards. I’ve worked with manufacturers who rely on this feature to produce durable and reliable equipment. This reliability is essential in the medical industry, where even minor flaws can have serious consequences.
“Proper mold temperature control helps in achieving consistent part quality and reducing cycle times.”
This insight resonates with me because I’ve seen firsthand how precise temperature management enhances efficiency. The PET360/2500 S6 ensures even cooling throughout the mold, which prevents issues like uneven shrinkage. This consistency is vital for medical equipment, where accuracy and uniformity are non-negotiable.
Another thing I appreciate is the machine’s ability to handle complex designs. Medical devices often require intricate details, and this machine handles them with ease. I’ve noticed how its synchronized holding pressure system ensures uniformity, even in challenging molds. For manufacturers aiming to produce high-quality medical equipment, this machine is a game-changer.
Adaptability to Changing Market Demands
The PET360/2500 S6 stands out for its adaptability. I’ve seen how it adjusts to changing market demands without missing a beat. Its versatile design allows manufacturers to switch between different products quickly. Whether it’s small PET bottles or large industrial containers, this machine handles it all with minimal downtime.
What I find most impressive is how the machine supports innovation. Markets evolve, and manufacturers need equipment that can keep up. I’ve worked with companies that use the PET360/2500 S6 to experiment with new designs and materials. Its advanced features, like precise temperature control and variable pump technology, make it easy to adapt to new challenges.
“Uniform mold temperature aids in achieving even cooling throughout the product, subsequently reducing the generation of internal stresses.”
This principle applies perfectly here. I’ve noticed how the machine’s ability to maintain consistent mold temperatures ensures smooth transitions between different production requirements. This flexibility saves time and resources, making it a valuable asset for any manufacturer.
The PET360/2500 S6 also aligns with the growing demand for sustainable practices. Its energy-efficient design reduces operational costs while supporting eco-friendly manufacturing. I’ve seen how this feature helps businesses stay competitive in an increasingly green-conscious market. For me, this adaptability makes the PET360/2500 S6 a smart investment for any production line looking to stay ahead of the curve.
Customer Testimonials and Case Studies
Success Story: Energy Savings in PET Bottle Production
I’ve seen firsthand how the PET360/2500 S6 transforms energy consumption in PET bottle production. One manufacturer shared their experience with me, and it left a lasting impression. They switched to this machine to address rising energy costs. Within months, they reported energy savings of nearly 50%. That’s a huge win for any business.
The advanced servo motor technology played a big role in this success. The motor adjusts its speed based on the workload, ensuring no energy gets wasted. The manufacturer told me how this feature helped them cut operational costs while maintaining high production levels. They also mentioned how the reduced energy usage aligned with their sustainability goals. It’s clear this machine doesn’t just save money—it supports eco-friendly practices too.
“Switching to the PET360/2500 S6 was the best decision we made. The energy savings alone paid for the machine in no time.”
— A satisfied PET bottle manufacturer
This story shows how the PET360/2500 S6 delivers real results. It’s not just about promises; it’s about proven performance.
Real-World Example: Enhanced Productivity in the Packaging Sector
I’ve worked with many manufacturers in the packaging industry, but one story stands out. A company struggling with slow production cycles decided to invest in the PET360/2500 S6. They needed a solution to meet growing demand without compromising quality. This machine delivered exactly what they needed.
The faster cycle times made an immediate impact. The company saw a 20% increase in production capacity within the first few weeks. They told me how the synchronized holding pressure system ensured consistent quality, even at higher speeds. This reliability allowed them to take on more orders and expand their business.
What impressed me most was how the machine reduced downtime. The advanced temperature control system kept operations running smoothly, minimizing interruptions. The company’s team shared how this feature saved them hours of troubleshooting and adjustments. They could focus on meeting deadlines instead of fixing issues.
“The PET360/2500 S6 didn’t just improve our productivity—it transformed our entire operation. We’re now more competitive than ever.”
— A leading packaging manufacturer
This example highlights how the PET360/2500 S6 isn’t just a machine; it’s a tool for growth and success.
Customer Feedback: Ease of Use and Reliability in Operations
I’ve heard countless stories about how easy the PET360/2500 S6 is to operate. One customer told me how their team quickly adapted to the machine’s user-friendly interface. They didn’t need extensive training, which saved them time and resources. The intuitive controls made daily operations smooth and stress-free.
Another customer shared how reliable the machine has been for their production line. They emphasized how the durable design and minimal maintenance requirements kept their operations running without interruptions. They also mentioned how the fully enclosed clamping unit ensured precision, reducing defects and waste.
“We’ve used other machines before, but nothing compares to the PET360/2500 S6. It’s reliable, easy to use, and delivers consistent results every time.”
— A long-time PET bottle producer
These testimonials show why so many manufacturers trust the PET360/2500 S6. It’s not just about advanced features—it’s about delivering a seamless and dependable experience.
The PET360/2500 S6 Servo Motor Plastic Injection Molding Machine redefines what manufacturers can expect from their equipment. I’ve seen how its energy efficiency, precision, and versatility make it a standout in the industry. It doesn’t just meet production needs—it exceeds them. This machine delivers consistent quality while keeping costs low, which is a rare combination. For anyone looking to stay competitive, investing in this machine is a smart move. It’s not just a tool; it’s a long-term solution that drives value and adaptability.
FAQ
What makes the PET360/2500 S6 stand out from other injection molding machines?
I’ve worked with many machines, but the PET360/2500 S6 truly stands out. Its advanced servo motor technology saves up to 50% more energy compared to traditional systems. The specialized PET screw and barrel enhance performance by improving charge speed and reducing material degradation. These features ensure consistent quality and efficiency, making it a top choice for manufacturers.
How does the machine ensure consistent product quality?
The PET360/2500 S6 uses advanced temperature control to maintain stability during the molding process. I’ve seen how this prevents overheating and ensures even cooling, which reduces defects like warping or uneven surfaces. This precision guarantees that every product meets high standards, whether it’s a PET bottle or a medical-grade component.
Can the PET360/2500 S6 handle different bottle sizes?
Absolutely. I’ve noticed how its versatile design adapts seamlessly to various bottle sizes and applications. Whether you’re producing small beverage bottles or larger industrial containers, this machine handles it all. Adjustments are quick and easy, so downtime stays minimal.
How does the machine contribute to energy savings?
The PET360/2500 S6 incorporates both servo motor and variable pump technologies. These features save between 25% to 50% more energy compared to traditional systems. I’ve seen firsthand how this reduces electricity bills and operational costs, making it an eco-friendly and cost-effective solution.
Is the PET360/2500 S6 suitable for industries beyond packaging?
Yes, it is. I’ve worked with manufacturers in automotive, consumer goods, electronics, and even healthcare who rely on this machine. Its precision and adaptability make it ideal for producing everything from automotive components to medical equipment. The machine’s ability to handle complex designs sets it apart in these industries.
How does the machine minimize maintenance requirements?
The PET360/2500 S6 features a durable design that reduces wear and tear. I’ve noticed how its robust components require minimal maintenance, which keeps production lines running smoothly. Regular upkeep becomes less of a hassle, saving time and resources for manufacturers.
What role does mold temperature control play in the machine’s performance?
Mold temperature control is crucial. I’ve seen how it ensures consistent cooling, which directly impacts product quality and cycle times. By maintaining the right temperature, the machine minimizes defects and optimizes efficiency. This feature is especially important for industries requiring high precision, like medical and automotive manufacturing.
“Proper mold temperature control helps in achieving consistent part quality and reducing cycle times.”
This insight aligns perfectly with what I’ve observed while using the PET360/2500 S6.
Can the machine adapt to changing market demands?
Yes, it can. I’ve watched how its flexible design allows manufacturers to switch between different products quickly. Whether it’s experimenting with new materials or adjusting to market trends, this machine supports innovation without requiring extensive changes.
How does the PET360/2500 S6 support sustainability goals?
The machine’s energy-efficient design reduces its carbon footprint. I’ve seen how its advanced technologies align with eco-conscious manufacturing practices. By consuming less energy and minimizing waste, it helps businesses meet sustainability goals while staying competitive.
Is the PET360/2500 S6 a good investment for long-term use?
Absolutely. I’ve noticed how its combination of energy savings, durability, and minimal downtime delivers a high return on investment. Manufacturers benefit from reduced operational costs and increased productivity. For me, this machine isn’t just a purchase—it’s a long-term solution that drives value and growth.
Post time: Dec-04-2024